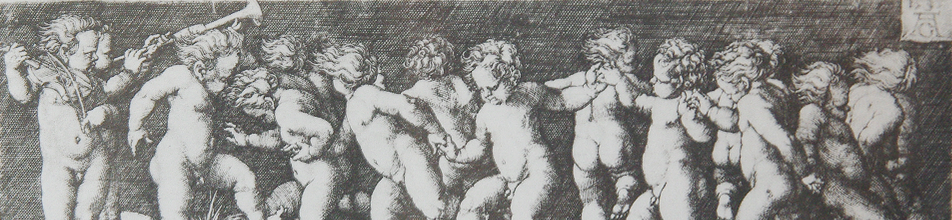
Introduction | The Precious Printing Process | Workflow Description | Example Images | Contacts, Links & Sources
Article on the Workflow
Heliogravure – Restoration and preservation of graphics using autotype printing This report describes an old printing technique which I have used to restore and preserve graphics, using autotype printing. The heliogravure, also known as photogravure, was invented by Karl Klic (1841-1926) in 1878 and had become widespread by the turn of the century. However, in spite of its excellent characteristics, this technique became almost completely forgotten. Taking copper engraving as the main example, I shall show how this procedure can be applied and describe the technical steps that are required. Copper engravings are found in many collections and may be regarded as “special” for a number of reasons:
Procedure In the past, black-and-white halftone slides were required that had been created from a negative and were the same size as the original. Large repro cameras were used, but films are no longer made in these dimensions. One possible alternative for smaller formats is X-ray film, but it seems reasonable to assume that these too will not be available in the long term. For these reasons, one has to use more “modern” procedures with the aim of generating an equivalent slide positive. The procedure is as follows: The original is scanned using SilverFast. The resolution should be “300dpi”. As some of the originals are quite large, I have chosen a flat-bed scanner that allows the original to be scanned in sections, which can then be reassembled using suitable software at a later date. SilverFast enables excellent shadow detail in greyscale mode, which is vitally important in the field of copper engraving. Sometimes the misapprehension exists that copper engravings are line originals. However, if one looks closely at the prints, it becomes clear that the dark lines are actually graded, and thus have to be reproduced in a similar way. Copper printing plates were once inked with pigments that were rich black, but in fact comprised of other colors such as green. Thus, the print is actually strictly speaking an RGB-image. Moreover, the RGB-mode offers another essential advantage: many old engravings show marks of different colors that have developed over the years. These are “eliminated” using complex filter technology: the original is examined through a range of gelatine filters to determine the “color cast”. Film material had to be panchromatic, which made further processing difficult. Today, a RGB-original provides every opportunity for quick and easy removal of such “color blemishes”. Furthermore, during the scanning process it is possible to “reconstruct” highlight and shadow masks, which in the past were created by laboriously superimposing half-tone- and lith films. After scanning, the image can be further improved, in this case using SilverFast HDR. By accessing the processed file, a slide positive is produced using an imagesetter. In order to reach the quality formerly achieved by half-tone films, a frequency-modulated screen is used that reproduces the half-tone character well. Please note that “FM screening” gives a different tonal gain and thus extensive gradation changes are necessary before the photographic printing process. In certain cases, these special screens are generated with Fogra’s old Velvet Screen program. Torrent RIP and a Heidelberg imagesetter complete the workflow. If this equipment is not available then the FM screens could also be made by an outside contractor. The further procedure is identical to previous processing. It is interesting to note in this context that the etching process is similar to half-tone positives, despite the fact that the tonal area actually consists only of small black “dots” with a size of 20 micrometres, randomly distributed on the clear film area. ![]() Linting Bitumen dust is swirled in a large cabinet. A plate is inserted and after a few minutes is covered with a deposit of dust, which is so fine that it is barely visible to the naked eye. The dust is surface-fused to the plate by a heating process. After this process, half of the surface should be covered. If the plate is held at an angle to the light, it has a velvet colored appearance. The back of the plate is covered with bitumen lacquer. When a plate prepared in this way is put into an etching bath (ferric chloride), the etching reagent penetrates the dust-free areas and creates depressions in the surface of the plate. Depending on the duration of the etching process (up to 10 minutes is common) plates like this can be used to print the full range of greyscales in the form of linked, single-colored surfaces. Half-tone generation In order to accommodate all existing half-tones simultaneously on one plate, the ferric chloride has to react with the relevant parts of the dust-coated copper plate for varying amounts of time. In order to produce this, a pigment copy is used which is made on pigment paper or film. This medium consists of stiff paper with an infused red gelatine coat. As this material is also used by modern printing presses, fortunately it is still available. The paper is bathed in a cold potassium dichromate solution (3%) and made light-sensitive; it is then exposed under the slide (pigment copy). Formerly, these exposures were made using sunlight – which explains the name of the process (heliography literally means “sun writing”). Today, powerful point light sources are used, featuring beneficial spectral characteristics, such as xenon light, carbon arc lamp etc. The light shining through the slide acts with varying intensity on the gelatine coat of the paper. In this way, the areas that have been exposed to light loose the capacity to dissolve in warm water, completely or in part. Previously, many photographic processes, such as pigment printing, exploited this phenomenon. After exposure and with the help of distilled water, the copy is rolled onto the coated plate, the gelatine facing the plate. The plate is “developed” after approximately 15 minutes in warm water at a temperature of around 40°C. Those parts of the gelatine that do not become hard are dissolved. The result is a depression-like negative copy of the slide: the gelatine is dissolved from the black areas and hardened on the white areas of the slide. For the grey values, the gelatine is proportionally reduced, depending on the intensity of exposure. Etching Ferric chloride solution contains water, which is absorbed by gelatine. Depending on the thickness of the gelatine coat, times vary until the ferric chloride reaches the copper and starts etching where no coated grain is present. This means that different parts of the plate are etched for different lengths of time for any given time interval. The overall etching time has to be adjusted so that the coat that is penetrated first is the same as the darkest tones in the original. In order to speed up the etching process, several ferric chloride solutions are used, at different dilutions. The water content determines the specific weight of the solution, expressed in Baumé degrees. The etching process is carried out in baths at 40 Baumé degrees. Four baths are sufficient. In principle, it is possible to etch in a single bath, which is what happens when making cylinders for rotary printing. However, the etching process is easier to manipulate if carried out using several baths and this method should be preferred. The plate is rinsed and cleaned after the etching process. The grain is also removed with solvents (Toluol). Some corrections, such as touch-up, post-etching etc., might have to be carried out before printing. The final result looks like this: the plate is covered with endless fine depressions and the original is visible when the plate is held at an angle to the light. To sum up the workflow:
The steps described above make it clear that the heliogravure is not an easy technique, but a complex one. However, it delivers results which are gratifying. Using this technique, it is possible to reproduce any original generated by gravure printing in the most faithful way – such print quality cannot be approached by any other process. Two quotes from different times provide a hint: “...Photogravure… (also called Lichtkupferstich), which is also able to reproduce half-tones, is the most perfect photomechanical procedure, its products hold all of the softness and delicacy of mezzotint engraving or aquatint etching...” [from Herdes Konservationslexikon, 3rd Edition, Band IV, Page 318, Munich 1905, under the keyword “Heliographie”]. In the catalogue to the exhibition „From Delacroix to Munch, art prints in the 19th century” [Von Delacroix bis Munch, Künstlergraphic im 19ten Jahrhundert], the description on page 172 of a gravure by Karl Klinc reads: “the velvety effect of dark tones is done to perfection”. While applying heliogravure in practice, one might notice that this technique has the potential to be suitable also for reproducing pages generated by other methods, such as charcoal drawings, woodcut etc. Hopefully, these explanations have inspired interest in this technique. Figure 1: Copper engraving by Heinrich Aldegrever (1536). The original is in the City Museum of Münster, Germany. The print is a unique specimen. Condition: the page is heavily soiled; some marks completely cover parts of the image. The colour of the marks is similar to the print. Some parts of the image are badly affected: top right page, missing letters top left etc. Restoration of the original page appears problematic as the condition of the paper is poor. Procedures previously carried out: detailed half-tone retouching of the slide to remove or reduce marks that disrupt the image. Restoration of the deep depression drawings that are partly missing due to marks and stains. Insertion of missing letters (top left), restoration of damaged line layout (right half of image). All work was carried out based on information that was recovered with difficulty from the residual image. Figure 2: Sample print. The sample print was made on standard copper print handmade paper without applying any correction. Brown/ rich black was chosen as the colour. There is no need for further corrections applied directly to the plate. Figure 3: Detail from Figure 2. |
Introduction | The Precious Printing Process | Workflow Description | Example Images | Contacts, Links & Sources